PET Preform Bottle Blowing Machine
PET Preform Bottle Blowing Machine

Key Features
High Efficiency and Output: 2000-20000BPH
Fast Production Rates: Capable of producing a high volume of bottles per hour, ensuring optimal productivity.
Continuous Operation: Designed for long-term, continuous use with minimal downtime.
Advanced Blowing Technology:
Precision Molding: Utilizes advanced molding technology to produce bottles with consistent quality and uniform thickness.
Versatile Bottle Sizes: Easily adjustable to produce bottles of various sizes, from 500ml to 2000ml.
Energy Efficiency:
Low Energy Consumption: Incorporates energy-saving technologies to reduce power usage without compromising performance.
Efficient Heating System: Advanced heating systems ensure uniform heating of preforms, improving bottle quality.
User-Friendly Design:
Intuitive Control Interface: Features a touch-screen control panel for easy operation and monitoring.
Quick Changeover: Designed for quick and easy mold changeovers, minimizing downtime and enhancing flexibility.
Robust Construction:
Durable Components: Built with high-quality materials to ensure long-term reliability and durability.
Low Maintenance: Requires minimal maintenance, reducing operational costs and maximizing uptime.
Quality Assurance:
Consistent Quality: Ensures each bottle meets strict quality standards, with uniformity in shape and thickness.
Defect Detection: Integrated systems to detect and reject defective bottles, ensuring only the highest quality products are produced.
Our Advantages
- User-Friendly
- Food Grade Material
- High-Efficiency
- Energy Efficiency
- Low Energy Consumption
- Advanced Technology





Pre-sales Advice
Our Pre-sales Consultation Services Are Designed To provide You With All The Information.
Installation Service Provided
Online Service And Enginner Oversea Service
Deliver Time
20-60 Days After Receiving The Deposit
Main Technical Parameters
Model | Unit | HG–A1 | HG-A2 | HG-B1 | HG-B2 | HG-C1 | HG-C2 | HG-C3 | |
Clamping System | Number of cavities | cavities | 2 | 2 | 4 | 4 | 6 | 6 | 8 |
Clamping force | KG | 35000 | 45000 | 40000 | 48000 | 56000 | 65000 | 75000 | |
Mold stroke | mm | 90 | 125 | 90 | 125 | 90 | 125 | 90 | |
Stretching stroke | mm | 260 | 330 | 260 | 330 | 260 | 330 | 260 | |
Bottom stroke | mm | 50 | 50 | 50 | 50 | 50 | 50 | 50 | |
Central distance | mm | 76.2 | 114.3 | 76.2 | 114.3 | 76.2 | 114.3 | 76.2 | |
Number of preform holder | PCS | 68 | 68 | 96 | 96 | 106 | 106 | 126 | |
Made Container | Max.container volume | ml | 600 | 1500 | 600 | 1500 | 600 | 1500 | 600 |
Max.container height | mm | 260 | 330 | 260 | 330 | 260 | 330 | 330 | |
Max.container diameter | mm | 68 | 105 | 68 | 105 | 68 | 105 | 68 | |
Max.prefrom height | mm | 100 | 140 | 100 | 140 | 100 | 140 | 120 | |
Max.neck diameter | mm | 38 | 38 | 38 | 38 | 38 | 38 | 38 | |
Theoretical Output | B/Hr | 2500 | 2000 | 4500 | 4000 | 7200 | 5000 | 10000 | |
Electrical System | Number of heating oven | PCS | 2 | 2 | 4 | 4 | 6 | 6 | 6 |
Number of lamp | PCS | 2×8 | 2×8 | 4×8 | 4×8 | 6×8 | 6×8 | 6×8 | |
Heating power | KW | 24 | 48 | 56 | 72 | 64 | 96 | 96 | |
Installed power | KW | 26 | 50 | 60 | 80 | 69.5 | 100 | 100 | |
Voltage ( or Customization) | Voltage | 380V/50HZ | 380V/50HZ | 380V/50Hz | 380V/50Hz | 380V/50HZ | 380V/50HZ | 380V/50HZ | |
Air System | Operating pressure | mpa | 0.7-0.9 | 0.7-0.9 | 0.7-0.9 | 0.7-0.9 | 0.7-0.9 | 0.7-0.9 | 0.7-0.9 |
Blowing pressure | mpa | 2.5-3.0 | 2.5-3.0 | 2.5-3.0 | 2.5-3.0 | 2.5-3.0 | 2.5-3.0 | 2.5-3.0 | |
High pressure air consumption | L/min | 2.4/30 | 2.4/30 | 3.6/30 | 4.0/30 | 6.0/30 | 8.0/30 | 8.0/30 | |
Chiller System | Temperature | 9-13 | 9-13 | 9-13 | 9-13 | 9-13 | 9-13 | 9-13 | |
Pressure | Mpa | 0.4 | 0.4 | 0.4 | 0.4 | 0.4 | 0.4 | 0.4 | |
Rated power | HP | 3 | 5 | 5 | 8 | 8 | 10 | 15 | |
Machine | Machine dimension | M | 2.5X1.5X20 | 3.0X1.5X20 | 3.6×1.5×2.2 | 3.6×2.2×2.2 | 4.0×2.1×2.2 | 5.8×2.1×2.2 | 5.8×2.1×2.2 |
Machine weight | KG | 2000 | 2500 | 3500 | 4500 | 6000 | 7000 | 7000 |
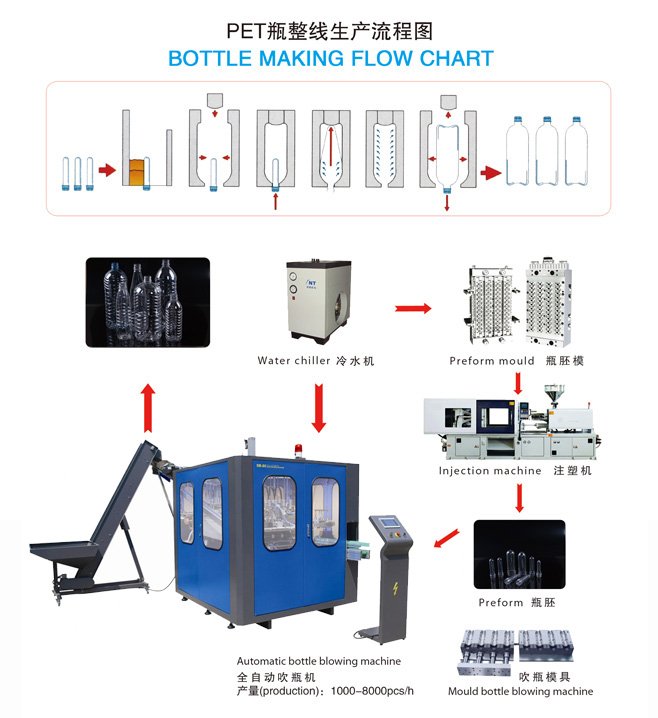